Resources for Enhanced Manufacturing Operations
Manufacturers today face the complex challenge of balancing efficiency with innovation. With advancements in technology rapidly altering the industrial landscape, there’s a continuous need for resources that can empower manufacturing operations. To stay competitive and maintain streamlined processes, it’s critical to integrate advanced tools and methodologies. These can range from automation to lean manufacturing techniques, and they offer a suite of benefits aiming to optimize production and decrease waste. Below, we’ll explore key resources designed to enhance manufacturing operations for businesses aiming for the next level of operational excellence.
Exploring the Role of Automation Tools in Streamlining Manufacturing Processes
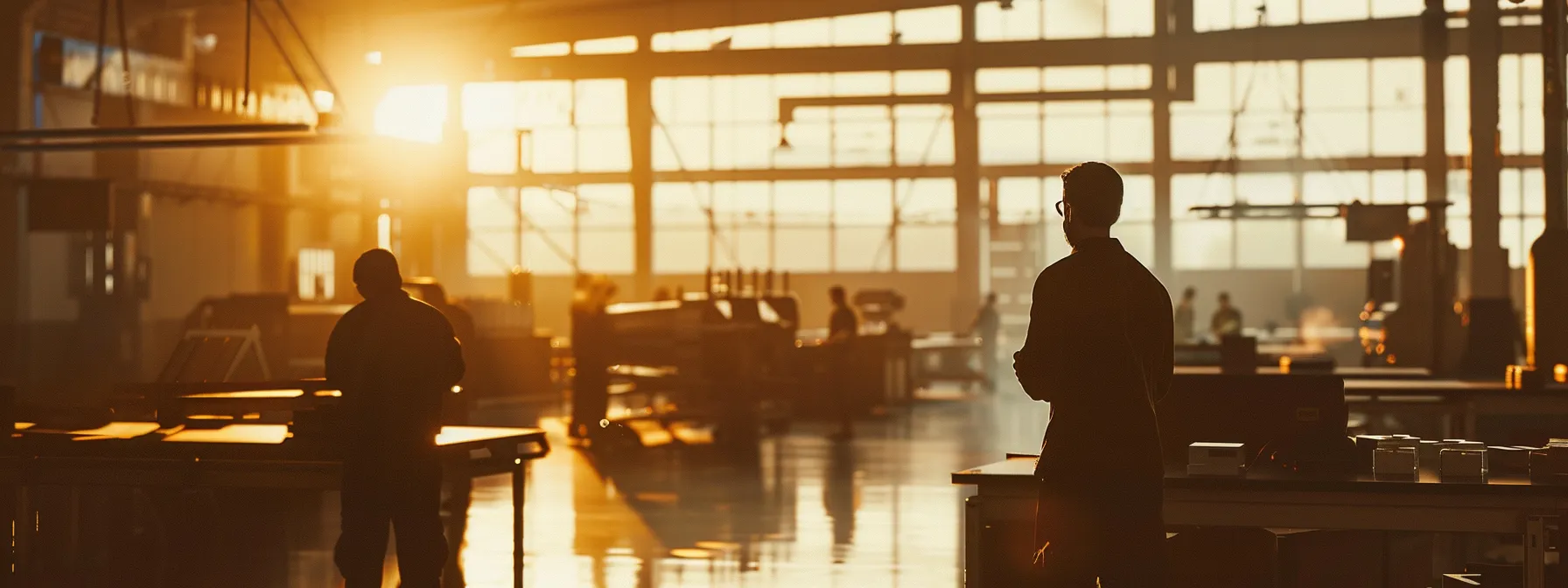
Automation in manufacturing has transformed production by boosting efficiency and quality. Robotic systems and conveyor belts ensure non-stop operations, reducing errors and fatigue. These tools allow workers to focus on higher-skilled tasks, improving job satisfaction. Software solutions like mycoi enhance operational certainty and compliance, helping manufacturers meet rigorous standards.
Adopting automation requires a strategic approach to select the right tools for specific tasks, such as assembly or packing. Manufacturers that blend automation with human expertise lead the industry, setting benchmarks for others. A culture of continuous improvement and technological investment, supported by platforms like OTTO Seo, keeps companies ahead in a competitive market.
Implementing Lean Manufacturing Techniques for Efficiency
Lean manufacturing is a philosophy that focuses on maximizing value while minimizing waste. It involves value stream mapping and continuous improvement, allowing businesses to critically evaluate each production step. Lean manufacturing promotes ‘less is more’ resource utilization, advocating for ‘Just-in-Time’ production, where inventory is pulled based on customer demand, reducing capital tied up in raw materials and finished goods.
Lean also empowers employees to identify inefficiencies and suggest improvements, fostering a more engaged workforce. Implementing lean manufacturing is a continuous journey, requiring ongoing education, training, and process evolution. Each small improvement builds towards significant gains in efficiency, quality, and customer satisfaction over time. This approach fosters a more engaged and productive workforce, allowing companies to take ownership of their success.
Utilizing Advanced Analytics for Predictive Maintenance in Manufacturing
The manufacturing industry is adopting predictive maintenance, powered by advanced analytics, to prevent downtime and ensure optimal performance. This proactive approach uses data from equipment to predict when maintenance should be performed, allowing manufacturers to schedule maintenance during non-critical production periods.
Sensors in machines report their health status, allowing advanced analytics to interpret wear and tear predictions. This not only prevents unplanned downtime but also minimizes the cost of urgent repairs and replacements. However, integrating advanced analytics can be complex, so companies often partner with tech experts to optimize their online presence and understand predictive trends.
The Impact of Industrial IoT on Real-Time Monitoring and Control
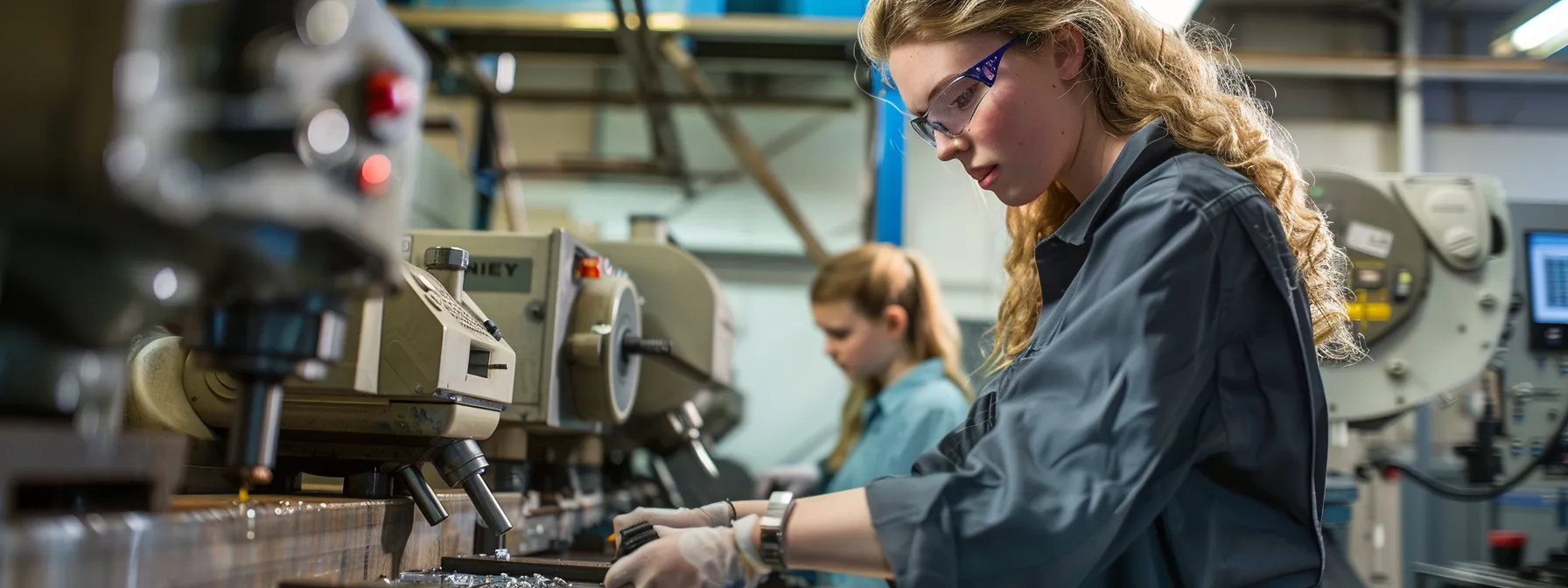
The Industrial Internet of Things (IIoT) has revolutionized manufacturing operations by providing real-time data on machinery performance, enabling immediate adjustments to optimize production cycles and reducing waste. This connectivity fosters improved production insights, enhanced communication across different plant units, and synchronized efforts.
IIoT systems also ensure worker safety by alerting staff to equipment malfunctions or stray operating parameters, promoting proactive hazard management. The transition to a fully connected system represents a significant change in operations, necessitating manufacturers to train staff and reshape processes to fit this new, data-rich framework.
Training and Development: Equipping Employees with the Skills for Advanced Manufacturing Operations
Manufacturing enterprises rely on their workforce, and continuous training and development are crucial for ensuring proficiency in advanced operations. Training programs provide employees with the confidence to operate complex machinery, use sophisticated software, and adapt to new processes. Investing in the workforce goes beyond technical skills, nurturing leadership, problem-solving, and communication abilities.
A multifaceted training approach ensures a well-rounded team ready to support modern manufacturing operations. Manufacturers that recognize the importance of training are seen as leaders in innovation and productivity. By fostering a culture that values constant learning and skill development, these companies can thrive in a rapidly changing industrial landscape.
Overall, the efficient and forward-thinking use of technological resources and methodologies lays the groundwork for a successful manufacturing operation. Advances in automation, lean manufacturing, analytics, and IoT, coupled with ongoing employee development, are the keystones of modern production. They constitute a blueprint for a resilient, future-proof manufacturing enterprise capable of adapting to the ever-shifting demands of global markets and consumer expectations.